HomeInverter knowledge
Installing a frequency inverter on industrial motors remains one of the
best and most straightforward ways of reducing energy usage,
particularly when driving pumps and fans. Frequency inverters can cut
the energy bill on an application or system by more than their own
capital cost in a relatively short period.
As electricity prices continue to rise, the return on investment (ROI) on a frequency inverter application increases in proportion to the bill. Furthermore, because the cost of a frequency inverter has actually remained stable over the last decade, payback can be more quickly achieved, often in less than a year.
As electricity prices continue to rise, the return on investment (ROI) on a frequency inverter application increases in proportion to the bill. Furthermore, because the cost of a frequency inverter has actually remained stable over the last decade, payback can be more quickly achieved, often in less than a year.
The prime and immediately tangible target for saving energy using frequency inverters is old mechanical systems, typically using centrifugal pumps and fans, that vary the flow of either water or air in a building or industrial facility. To identify, frequency inverter manufacturers are making it as easy as possible to calculate possible savings, providing PC and even iTunes applications in addition to the know-how for doing the quick hand calculations on-the-spot to quantify potential energy savings.
Three phase harmonic compensated line or load reactors allow one to "clean up" the voltage being sent to the motor from a frequency inverter. Harmonic compensation maximizes the reactor's benefit to the frequency inverter input circuit, while PWM / IGBT protection maximizes their performance in the frequency inverter output circuit. A purer voltage to both the frequency inverter and the motor means:
Putting a contactor on the output of the frequency inverter will assure immediate removal of voltage from the motor which is what you want. On the other hand, some inverters are easily damaged by switching on their output and that it's possible that the motor could be reconnected to the output of an inverter that was operating above zero frequency and this could also damage the inverter. (Effectively a direct (non-soft) or full-voltage start on the output of a frequency inverter)
Flux vector frequency inverters use a method of controlling torque similar to that of DC drive systems, including wide speed control range with quick response. Flux vector frequency inverters have the same power section as all PWM frequency inverters, but use a sophisticated closed loop control from the motor to the frequency inverter's microprocessor. The motor's rotor position and speed is monitored in real time via a resolver or digital encoder to determine and control the motor's actual speed, torque, and power produced.
Applying a frequency inverter to a specific application is no mystery when you understand the requirements of the load. Simply put, the frequency inverter must have ample current capability for the motor so that the motor can produce the required torque for the load. You must remember that machine torque is independent of motor speed and that load horsepower increases linearly with rpm.
Reflected waves caused by a cable-to-motor impedance mismatch are prevalent in all frequency inverter applications. The magnitude of the problem depends on the length of the cable, the rise-time of the PWM (pulse width modulated) carrier wave, the voltage of the frequency inverter, and the magnitude of the impedance difference between the motor and cable.
Among the most successful strategies managers have at their disposal for controlling electrical energy use and minimizing utility costs is the use of frequency inverters. Incorporating frequency inverters into applications such as fans, pumps, and cooling towers can reduce energy use up to 50 percent at partial loads by matching motor speed to the changing load and system requirements.
Frequency inverter provides dramatic energy savings by optimizing the system, not by improving the actual efficiency of the motor in isolation (as an energy efficient motor retrofit would). In fact, a Frequency inverter system is about 4% to 6% less efficient at full load than an induction motor alone. This is mainly due to the losses in the Frequency inverter itself. However, it doesn't take much operation at reduced load to save more energy than is lost at full load. Average loading as high as 90% can justify a Frequency inverter retrofit for high-duty applications.
Frequency inverters are used in any application in which there is mechanical equipment powered by motors; the inverters provide extremely precise electrical motor control, so that motor speeds can be ramped up and down, and maintained, at speeds required; doing so utilizes only the energy required, rather than having a motor run at constant (fixed) speed and utilizing an excess of energy.
Some manufacturers' inverters can provide 100% torque at Zero speed without an encoder. A properly rated and designed motor can be provided to operate at Zero speed, full torque (often called 1000:1 speed range motors). This is a very typical motor requirement for Paper Winders and Rewinders, and Steel Coilers and Uncoilers.
A single phase to three phase converter is a three phase star connected squirrel cage induction motor. It converts 380V single phase 50Hz (across UV input) to 380V three phase (UVW) with a slight unbalance (5%) in Voltage. It is used extensively on Indian railways 25kV 50Hz electric locomotives for driving 150kVA three phase motor load of auxiliary drives like compressors, blowers, pumps...........more than a dozen.
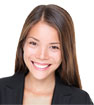
Search inverters
Category
inverters
Featured

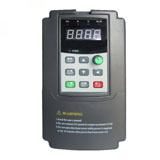
Recent
60Hz to 50Hz Frequency Converter
50Hz motor running on 60Hz power supply
Single phase to three phase converter
Frequency converter typical shortcomings
Frequency Converter Troubleshooting
Frequency inverter, the best energy saving solution
Does Frequency converter better than control valves in flow controls
Frequency Converter for Pumps
Why AC motor needs a Frequency Converter?
Determining frequency converter size
Frequency inverter energy efficiency calculation
Frequency inverter for heavy duty application (mining)
50Hz motor running on 60Hz power supply
Single phase to three phase converter
Frequency converter typical shortcomings
Frequency Converter Troubleshooting
Frequency inverter, the best energy saving solution
Does Frequency converter better than control valves in flow controls
Frequency Converter for Pumps
Why AC motor needs a Frequency Converter?
Determining frequency converter size
Frequency inverter energy efficiency calculation
Frequency inverter for heavy duty application (mining)